metal stamping china
Find metal stamping china for your business needs with ETCN. Explore our large selection of metal stamping services.
metal stamping
As a professional high-speed stamping press manufacturer, ETCN has several 15 to 315 tons of stamping and drawing equipment, a complete set of equipment for producing and processing metal products, and mature industrial metal stamping technology. It established a professional mold processing workshop with the ability to design and manufacture molds and to provide customers with better and custom metal stamping services.
ETCN custom CNC machining is the ideal sheet metal stampings and pressings Pvt ltd for sheet metal pressing.
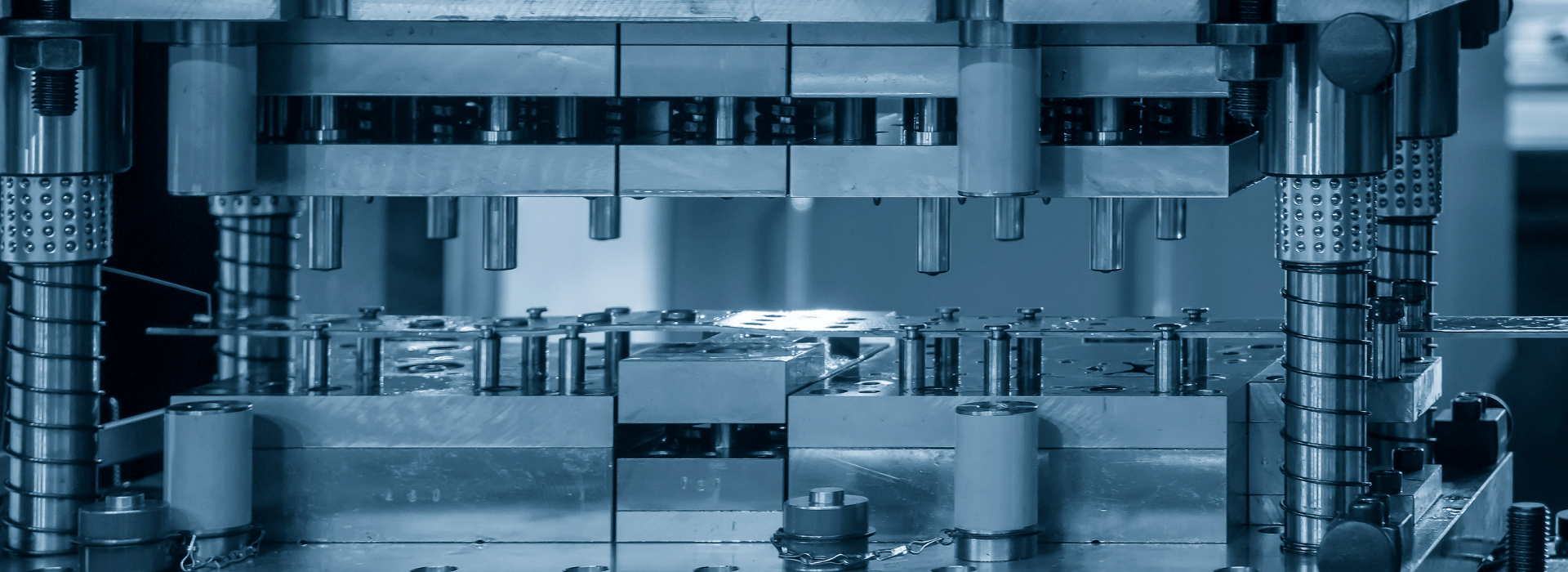
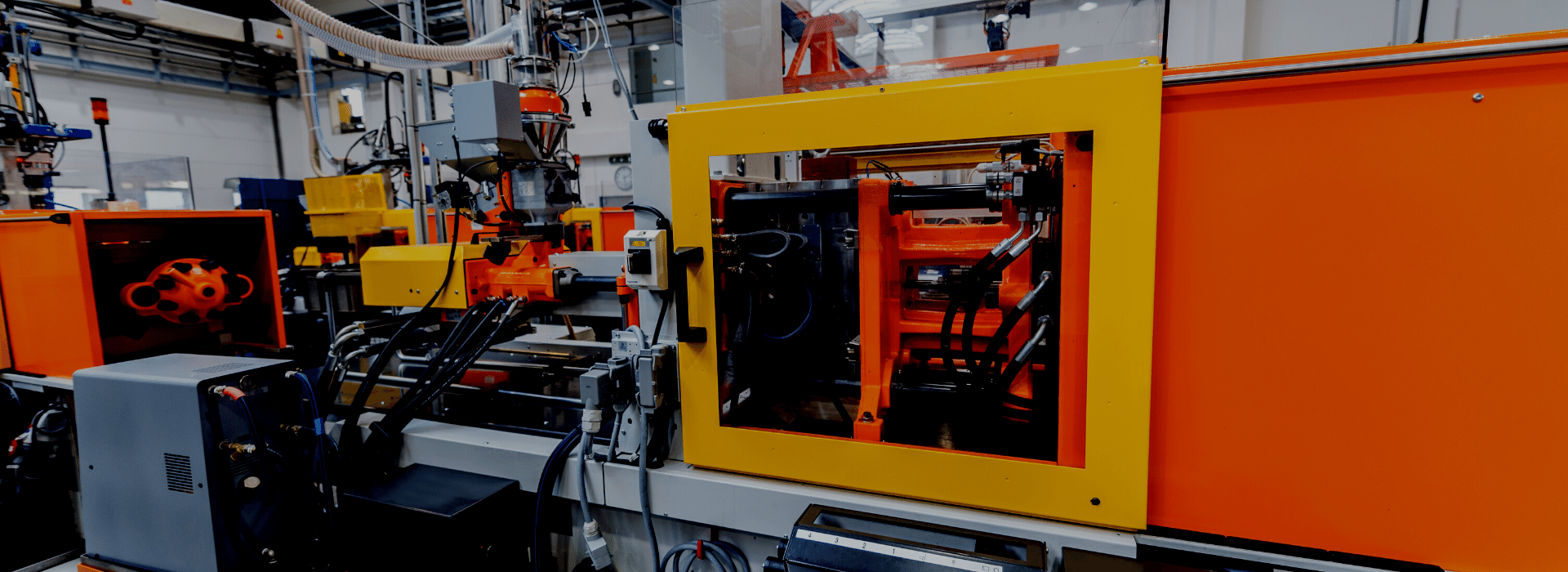
Explore our progressive die stamping with various designs and shapes ranging from 2D to 3D. From custom toolmakers, we can supply parts for die-stamping systems with various materials such as plastic, metal or steel.216 characters
Stretch forming is an advanced manufacturing process that uses a stretched metal sheet to create custom parts or products. Metal stamping is one of the most common techniques used for stretch forming because it allows for precise and consistent shapes to be formed from a wide range of materials.
What is the stamping process?
The stamping process is a manufacturing process used to create components from a single piece of metal. The stamping process begins by cutting the metal into the desired shape using a saw or a CNC machine. After the metal has been cut, it is machined to its final shape. This is done using a series of rotary and stationary tools that create precise, individualized shapes. Once the metal has been machined, it is stamped out using a press or an embosser.
metal stamping FAQs
Frequently Asked Questions.
What are the four type of metal stamping?
There are four main types of metal stamping: coining, embossing, die-stamping, and pressing.
Coining is the most basic form of metal stamping. It uses a small press to create small circular impressions in the metal. This is used to create coins, medals, tags, and other small pieces.
Embossing is similar to coining, but it uses a bigger press to create deeper impressions in the metal. This is used to create things like medals and tokens.
Die-stamping is similar to embossing, but the press creates more complex designs. This is used to create things like stamps and logos.
Pressing is the most advanced form of metal stamping. It uses a huge press to make large impressions in the metal. This is used to create things like car doors and frames.
What are the disadvantages of metal stamping?
Metal stamping is a widely used manufacturing process that creates parts from a metal piece by pressing it into a design. While the process has many advantages, there are also some disadvantages to be aware of.
One disadvantage of metal stamping is that it can be difficult to produce accurate parts. This is because the metal can deform and move during stamping, which can ultimately affect the finished product. Additionally, metal stamping often requires elaborate setups and machines, which can increase the cost of production.
Another disadvantage of metal stamping is that it can be time-consuming and labor-intensive. This is because the process often requires multiple steps, including drilling and machining, as well as stamping. Consequently, it can take longer to create a part using metal stamping than other manufacturing methods.
Overall, while metal stamping has its own set of advantages and disadvantages, it remains one of the most popular manufacturing processes out there. So if you’re looking for a fast and easy way to create custom parts, metal stamping may be the best option for you.
How does a metal stamping press work?
A metal stamping press is a machine that uses pressure and heat to create patterns or designs in metals. The machine has a series of dies that are pressed against the workpiece, which causes them to deform and create the desired design. Metal stamping presses are often used to create parts for cars, aircraft, and other industrial equipment.
The main problem with die-casting thin-walled products is that the material can easily crack when it cools. This can cause the part to fail when it’s used, so it’s important to take precautions when making them.
One way to prevent cracking is to use a thicker walled die. This will make it more difficult for the material to break apart, and it will also result in a stronger part. Another method is to use a thermal barrier material. This will help to keep the material from cooling too quickly, and it will also prevent cracks from forming.
If you’re die-casting thin-walled products, it’s important to take precautions to avoid cracking. By using a thicker walled die or using a thermal barrier material, you’ll be able to produce strong parts that won’t fail later on.
What products are made by metal stamping?
Products that are often made using metal stamping include car parts, medical implants, and jewelry. Metal stamping is a process of creating a three-dimensional object from a flat piece of metal by pressing it into various shapes. This process is used to create products that are both unique and durable.
Request a Quote
Do you need a quote for your high-precision part? Contact us now by phone, email, or through our contact form.