CNC Machining Service China
ETCN is a professional CNC machining company in China. We provide high-quality CNC machining services, including turning, milling, drilling, grinding, and other precision machining services. With many years of experience in the industry, we have established a good reputation among our clients. We are committed to providing our clients with high-quality products and services at competitive prices. If you are looking for a reliable CNC machining supplier in China, please get in touch with us today.
- #1 provide precision that is difficult to match using other manufacturing processes
- #2 faster than other production methods, reducing lead time and increasing customer satisfaction
- #3 creates versatile parts with multiple uses throughout different industries due to their customizable nature
Get Our Best Quotes
Please Fill in the Form Below and Our Engineers Will Respond within 24 Hours
Home » CNC Machining Service China
What is CNC Machining?
CNC machining is a manufacturing process used to produce precision parts and components. It stands for Computer Numerical Control and involves using computers to control machine tools such as drills, lathes, routers, grinders, and other cutting tools. The CNC machine is programmed with instructions on moving the cutting tools to create the desired shape or feature on a workpiece.
# How CNC machining works
CNC machining is typically used when producing high-precision parts with tight tolerances, such as medical implants and aerospace components.
Machines can produce complex geometries with extreme accuracy because they can be programmed to repeat operations multiple times. Even intricate shapes can be created consistently without having to reset the machine every time. Additionally, CNC machines can provide consistent quality because the same program is used each time the part is produced.
Due to their increased precision and speed, CNC-machined workpieces generally have superior surface finishes than those produced using traditional machining methods.
Furthermore, because these machines are automated, they require fewer operators than traditional machines, resulting in lower labor costs in production runs. However, one downside of CNC machining is that it requires an upfront investment for a machine and software development and training,, which must be considered when deciding whether or not this type of manufacturing process is right for your
# Advantages of CNC Machining
CNC Machining is a process that uses computer-controlled machines to shape and form materials into desired products. It offers many advantages to industrial businesses, particularly in terms of reducing cost and improving accuracy in the manufacturing process. Here are 10 advantages of CNC Machining for industrial services.
1. High Accuracy: CNC machining is extremely accurate when creating parts and components due to its precision cutting capabilities and high-quality control systems. This accuracy reduces waste while maximizing productivity, allowing for the production of high-quality goods with minimal effort.
2. Shorter Lead Time: Traditional manufacturing methods require numerous steps between design and finished product; CNC machining allows these steps to be condensed into a much shorter lead time. This allows manufacturers to produce goods more quickly, significantly increasing their efficiency and bottom line.
3. Improved Safety: By automation, there is less need for manual labor in CNC machining which minimizes human error and potential harm or accidents to workers on the production floor. This also reduces insurance costs associated with workplace injuries as well as compliance costs related to safety regulations.
4. Lower Skilled Labor Costs: As most CNC machines are automated, operators require minimal training compared to traditional methods of manufacturing that require higher skilled labor such as milling operators or drillers who must understand complex machinery operations and be able to troubleshoot potential issues during the production cycle.
5. Versatility: Unlike some traditional manufacturing processes, CNC machines can be adapted quickly for new products without significant retooling or setup time, allowing manufacturers to quickly switch from one product style to another based on fluctuations in customer demand or market conditions without losing momentum in the production cycle.
6. High Volume Outputs: The accuracy provided by CNC machining enables manufacturers to achieve higher levels of output per unit than traditional methods often allow for – meaning more profit per job completed with fewer personnel hours required for completion compared with other types of processing techniques used for large volumes of workpieces..
7 . Consistent Quality Control: Automated processes mean that quality control measures can be programmed directly into the machine’s operating functions, ensuring consistent quality standards every time regardless of operator skill level or changes in personnel staffing levels throughout the production cycle – resulting in consistently high-quality outputs at all times even if personnel changes occur during a project’s execution phase..
8 . Low Maintenance Costs : Automation means that there is little requirement for maintenance actions such as oil changes or periodic calibrations needed when using manually operated machinery which can significantly reduce overhead expenses associated with keeping machines operational at all times..
9 . Cost Savings : Compared with traditional manual processing techniques, CNC Machining requires fewer resources such as raw materials and personnel hours which translates into cost savings across many aspects of the manufacturing process from procurement through post-production support activities such as packaging and shipping..
10 . Increased Productivity : Automated processes not only increase efficiency but also boost productivity by reducing downtime due to machine jams or malfunctions which further increases profitability by eliminating costly delays associated with rework efforts caused by errors stemming from manual processes..
# What are the disadvantages of CNC machining?
Industrial CNC machining services have become increasingly popular in recent years. However, some drawbacks to using this technology should be considered when deciding whether or not to utilize a CNC machining service.
One of the major disadvantages of CNC machining is its relatively high cost. This is because the machinery used to create parts using CNC machining processes is extremely precise and usually costs thousands or more. It also requires highly-trained personnel to operate the equipment, which can also add to costs. In addition, due to the programming complexity used in the production process, there may be unexpected costs associated with reworking parts if errors occur during production.
Another disadvantage of CNC machining is its limited flexibility for prototyping and very small batch production runs. With traditional manual machining processes, it is possible to produce unique parts with custom features quickly and easily. However, this becomes difficult with CNC machines as programming and setup take much time and effort in these scenarios. While CNC machines are excellent for mass production runs, they do not offer the flexibility needed for rapid prototyping or low-volume orders that may require frequent changes throughout the development process.
Finally, although CNC machines can precise parts with a high degree of accuracy and repeatability, they still require human operators who possess advanced skill sets in ordertoy program and operate them correctly. This means that if inexperienced operators are tasked with operating these machines, they may cause mistakes that lead to costly redesigns or rejects during production.
Overall, while industrial CNC machine services offer many advantages, such as speed and precision when creating complex parts on a large scale, there are several potential risks associated with utilizing this technology, including costliness, lack of flexibility when it comes to prototyping/low volume orders and reliance on skilled personnel for successful operation.
CNC machining china factory
ETCN is a professional CNC machining china factory with rich experience producing high-precision parts. We use the latest equipment and technology to produce parts with tight tolerances and an excellent finish. Our parts are used in various industries, including aerospace, medical, and automotive. We are ISO 9001 certified, and our products meet or exceed all quality standards. Contact us today to discuss your requirements.
Why Use ETCN for Custom CNC Machining Services?
CNC machining is a highly specialized process that requires a great deal of precision and expertise. To ensure that your custom CNC parts are created with a high level of accuracy and produced quickly, it’s essential to find the right service provider for the job. ETCN offers the highest quality custom CNC machining services, providing clients with reliable, cost-efficient solutions tailored to their needs.
# extensive experience
ETCN’s team of experts has extensive experience in industrial CNC machining services, providing customers with accurate and efficient results. They specialize in producing high-precision components such as molds and dies, engine blocks, frames, brackets, etc. With years of practical experience in this field, they have established a well-organized production process that ensures all parts are made to exact specifications.
# accurate and efficient results
When you choose ETCN for your custom CNC machining needs, you can count on their experienced staff to create exactly what you need – quickly and accurately. In addition to their advanced facilities, they use state-of-the-art equipment, such as high-speed milling machines and robotic arms, which give them an edge over competitors in creating complex parts with tight tolerances at competitive prices. They also use advanced CAD/CAM software and other technologies to ensure that each part meets the exact requirements specified by the customer.
Overall, ETCN provides comprehensive industrial CNC machining services designed to meet customer requirements while keeping costs low. Their broad range of services includes rapid prototyping for concept models and large-volume production runs for commercial products. Their strict quality control procedures guarantee that all components will be delivered on time without defects or errors. This combination of experience and expertise makes ETCN an ideal choice for anyone who is looking for top-notch custom CNC machining services at competitive rates.
CNC custom machining
ETCN is a professional CNC machining service provider with rich experience in machining, milling, and turning. We are committed to providing customers with high-quality CNC machining services at competitive prices. With our advanced equipment and skilled technicians, we can ensure that your orders will be processed quickly and efficiently. Contact us today to get started!
CNC Milling Services China
CNC Milling Services is a process that uses computer numerical control (CNC) technology to machine parts and components from raw materials.
This process involves using a milling machine to cut away material to create a part or component’s desired shape and size. This process is often used when creating complex shapes and contours requiring high precision. It also offers better dimensional accuracy than other machining processes, which makes it a popular choice for industrial applications such as automotive manufacturing, aerospace engineering, medical device production, and much more.
# How CNC Milling Services works
CNC Milling Services utilizes cutting tools mounted on multiple spindles or other tooling systems to create 2-dimensional and 3-dimensional parts from raw materials such as metals, plastics, and composite materials.
These tools are programmed with specific instructions according to the design of the part or component that needs to be crafted. The CNC system then controls the motion of each tool along the X, Y, and Z axis to achieve the required result with accuracy, speed, and precision.
Depending on the complexity of the task at hand, this process will typically involve several spindle passes using various cutting tools to remove certain areas of material while leaving others intact — until all components have been machined down into their desired state.
# Advantages of CNC Milling Services
CNC (Computer Numerical Control) milling services are quickly becoming one of the most popular methods of manufacturing parts and components due to their precision, speed, and cost-effectiveness. Industrial CNC milling services offer a variety of advantages that can make them an ideal choice for some applications. Here are 10 of the top advantages that industrial CNC milling services provide:
1. Accuracy – With modern CNC equipment and software, parts can be machined to extremely precise dimensions with almost zero variation from one part to the next, ensuring a high-quality end product.
2. Efficiency – With automated machine operation, setup times can be minimized, and processes run faster than traditional manual machining techniques. This means less time on the production line, resulting in quicker turnaround times for your products.
3. Cost-Effectiveness – Many commercial operations benefit from the reduced material wastage associated with CNC machining and other cost savings, such as reduced labor costs. Reducing machine downtime also helps cut operating costs by maximizing machine utilization rates.
4. Versatility – Many materials can be cut using CNC milling machines, including aluminum, brass, stainless steel, and even plastics or composites. With a large selection of tooling available for specific processes, these machines can produce complex parts with intricate features that would otherwise require multiple steps on different machines or even manual labor.
5. Quality Control – Closely monitored tool paths and speeds help keep parts within tight tolerances while minimizing wear on cutting tools over long cycles; this ensures consistent results from part-to-part and job-to-job runs. Automated inspection systems can also measure individual parts during the machining process for additional quality assurance measures before shipment or assembly into finished products.
6. Repeatability – Once a program is entered into the system for a particular part design or feature, it is easy to reproduce identical results in subsequent runs; this eliminates any concerns about inconsistencies which can lead to costly rework down the road, further streamlining your production process and reducing overhead costs overall.
7 . Reduced Noise Levels – Unlike conventional mills, which create a loud noise when running, CNC machines are much quieter in operation, allowing them to fit into virtually any working environment without disruption or potential hearing loss issues due to excessive noise exposure levels over extended periods.
8 . Safety – Several safety features, such as guards around moving components, limit hazards during operation,, ensuring built-in safeguards for operators and bystanders alike.
9 . Flexibility – Many complex 3D shapes, tapers, curves, holes, pockets & grooves can be machined quickly & accurately on modern CNC equipment, ideal for those applications requiring intricately detailed work within tight constraints & demanding deadlines.
10 . Adaptability – As technology advances, so too do many types of machinery; upgrades like automatic tool changers & improved control systems make it easier than ever before to transition between jobs without sacrificing consistency or total productivity levels, giving you maximum flexibility when dealing with varying customer demands & ever-increasing industry standards …
# What are the disadvantages of CNC Milling Services
CNC Milling Services offer a range of advantages over traditional milling processes. However, industrial CNC Milling Services also has some potential disadvantages.
One significant disadvantage is the cost associated with these services. CNC milling machines are expensive to purchase and maintain, meaning that companies who outsource their CNC milling services will likely pay higher rates than they would for traditional manual milling processes. Additionally, the software required for programming can also be costly and time-consuming to learn. It could add additional expenses to the project if external help is needed to program the machine correctly.
Another major disadvantage of industrial CNC Milling Services is that they require more precision and accuracy than traditional manual methods. This means that any minor errors in programming, such as incorrect speeds or feeds, could result in major problems with the finished product, making it more difficult to achieve consistent results and requiring more time and effort to rectify any issues.
Finally, while CNC Milling Services are typically faster than manual machining processes, they can still take a considerable amount of time due to the need for precise cutting paths and finishing techniques. This means that larger projects may require multiple machines or longer machining times to complete them on schedule, which could add additional costs associated with labor and materials.
Overall, while industrial CNC Milling Services can provide several advantages such as greater accuracy, shorter lead times, and cost savings when compared with manual machining processes, these benefits must be weighed against the potential drawbacks of costlier equipment purchases, longer learning curves for programming software and increased lead times due to precise cutting paths and finishing techniques.
China CNC Turning Service
CNC (Computer Numerical Control) Turning Service is a highly specialized machining form that uses a computer-controlled lathe to shape and form metal and other materials into intricate and precise components. The CNC Turning process produces parts for various industries, including aerospace, automotive, medical device manufacturing, and consumer products.
# How CNC Turning Service works
The CNC Turning Service process begins with inputting specific machining instructions into the CNC machine. This can include commands such as cutting speed, feed rate, depth of cut, tool size, the material type being cut, and any requirements for the finished part.
After these parameters are set, the CNC machine will then use those instructions to rotate the workpiece at a predetermined speed while feeding the cutting tool against it. This accurately reproduces complex shapes and forms with consistent quality results every time.
CNC Turning Service requires programming knowledge to produce consistent results at its most fundamental level. A skilled programmer must understand how to enter settings that accurately reflect their desired specifications so that the machine can produce parts with consistent quality every time.
Once programmed correctly. However, the results can be extremely accurate and efficient, making this machining an ideal choice for high-precision parts requiring tight tolerances or intricate designs.
# What are the benefits over traditional methods
CNC turning service also provides many additional benefits compared to traditional methods, such as improved efficiency due to increased automation and reduced material waste due to more precise control over cutting parameters.
In addition, this method allows for complete repeatability between multiple parts produced from similar programs with minimal setup times, reducing the overall cost per part versus traditional methods like manual turning or milling operations.
CNC grinding service
CNC grinding service is a machining process that uses an abrasive wheel to remove material from the surface of a workpiece. This technique typically finishes, shapes, and deburr metal parts. It can also create complex parts with precise tolerances and intricate geometries. The process is highly accurate, with tolerances as low as + 0.0005” and repeatable results that are consistent over time.
# How precision CNC grinding works
CNC grinding service differs from conventional grinding in that it uses computer numerical control (CNC) machines to accurately control the grinders’ speed, power, and pressure during the grinding process. This ensures that each part has the same size, shape, and finishing as previous runs of the same part. Additionally, CNC grinding services often use automated loading and unloading systems which further increase accuracy by ensuring that the machine operator handles only one part at a time.
# Advantages of CNC grinding service
1. Speed and Accuracy – One of the key advantages of industrial CNC grinding services is the speed with which parts can be machined and the accuracy with which they are finished. CNC machines can precisely cut parts from a wide range of materials at high speeds, making them ideal for production runs where tight tolerances must be met.
2. Consistent Quality – By using numerical control (NC) programming, CNC grinding services can produce parts that always meet a consistent level of quality regardless of how many pieces are being produced or how complex the design is. This ensures that customers receive exactly what they expect when placing an order.
3. Versatility – CNC grinding services offer a wide variety of material options such as aluminum, brass, bronze, copper, iron, and plastic, This makes them ideal for making custom parts or components out of these materials in short or large production runs.
4. Reduced Labor Costs – Since CNC grinding services use automated machinery, there is no need for human operators to oversee the process and ensure quality control measures are met. This leads to significant savings in labor costs since only minimal personnel is required for supervision purposes during operation hours.
5. Automated Inspection Processes– Another advantage of industrial CNC grinding services is their ability to carry out automated inspection processes on each component produced before it leaves the machine shop floor, ensuring that all parts meet customer specifications before shipment or delivery. This eliminates costly rework on defective pieces and drastically reduces production times across the entire operation.
6. On-Demand Production – With various types of CNC grinding machines available today, manufacturers can choose from different models depending on their specific needs and requirements at any given time without having to make major investments in new equipment or machinery upfront.
7. High Precision Machining – Industrial CNC grinding machines have been designed to offer precision machining capabilities at levels previously thought impossible by traditional cutting techniques alone, resulting in reduced waste and increased efficiency overall when producing components from scratch or modifying existing designs using CAD/CAM software packages such as Solidworks and Autodesk Inventor 3D software suites respectively.
8 . Easier Setup Times – With newer generations featuring advanced features such as auto-tool calibration systems built into their design, setting up a CNC grinder typically takes significantly less time than other manual alternatives since operations can now be completed quickly with minimal effort required by operators.
9 . Increased Productivity & Efficiency – The combination of faster setup times and improved accuracy ensures higher productivity rates while also helping reduce operational costs related to wasted materials over longer production cycles due to errors or miscalculations made by human operators.
10 . Flexibility & Adaptability – Lastly, industrial CNC grinders offer superior flexibility and adaptability compared to manual versions due to their capacity for easily intricate programming instructions into their system to create more complex shapes than could ever be achieved through manual means alone.
# why choose ETCN
ETCN specializes in industries such as automotive or aerospace manufacturing, where high-precision parts are produced regularly.
CNC grinding services offer these businesses several advantages, such as improved accuracy and consistency of production, increased efficiency due to faster processing times, reduced wastage caused by inaccurate manual operations, and improved overall product quality due to precise finishes achieved on every part produced.
With demand for precision components continuing to rise across various industrial sectors,, the market for industrial CNC grinding services will likely likely remain strong over the coming years.
CNC Machining Tolerance
Maximum part size is an important aspect of CNC Machining. Maximum part size refers to the maximum dimensions that can be machined on CNC machines, including both milled and lathe parts.
For milled parts they can reach measurements up to 80” x 48” x 24” (2,032 x 1,219 x 610 mm), whereas lathe parts can be a length of up to 62” (1,575 mm) and a diameter of 32” (813 mm).
Maximum part size must be carefully evaluated when selecting a CNC machining process to ensure accuracy and efficiency throughout the production process.
A potential customer needs to decide upon the tolerances they desire while also understanding that they must balance those specifications with a realistic timeline for completion.
Fortunately, most CNC machining services advertise a standard lead time of 7 business days unless more complex and intricate customization is needed.
By setting this expectation up front, you can ensure that your project is delivered promptly and meets your requirements for precision and quality.
General CNC machining tolerances from metals and plastics/composites can be critical for many industrial applications. With Computer Numerical Controlled (CNC) machining, parts can be cut to precise specifications.
General tolerances for CNC machined metals are stipulated by ISO 2768, allowing an approximate +/- 0.005″ deviation from the stated measurement (+/- 0.127 mm).
Plastics and composites will have a greater allowable variation at approximately +/- 0.010″, providing designers with a certain degree of flexibility regarding accuracy in production pieces.
Precision tolerances are of utmost importance in CNC machining since the precision and quality of a component often depend on how accurately it is made according to the intended specifications.
At ETCN, we can understand and apply the specific drawings and GD&T callouts that your components require, with precision tolerances to ensure accuracy down to the finest details.
With our state-of-the-art machinery and years of experience, you can trust us to provide machined components with the highest level of accuracy and quality available.
Minimum Feature Size
Minimum feature size plays a vital role in CNC machining, which is important for accurate cutting and precision operations. This minimum feature size sets the standard for measuring components of the part and defining which features are attainable with CNC machinery.
Typically, the Minimum Feature Size of CNC machining is 0.020” (0.50 mm), though this number may change depending on factors such as material type and geometry of the project.
Through proper knowledge of Minimum Feature Sizes and their implications, designers can better understand what can or cannot be done during their machining project.
Threads and tapped holes can be tricky to engineer into precision pieces, but not for ETCN. We are equipped with CNC machining capabilities that allow us to manufacture threads and tapped holes accurately.
Threads can be cut in any standard size and custom-ordered sizes tailored to the specific needs of your project – however, these will require manual quote review.
With ETCN, all threading and tapping are performed with the same diligence expected from our jobs; we guarantee reliable results when you let us handle this important detail.
Edge condition describes how precise and clean a cut surface produced by CNC machining will be. Edge conditions for CNC machined parts can range from very smooth to sharp, penetrating edges.
To produce the highest level of precision, matching very tight tolerances, it is important to ensure that edge conditions are accurate and specified according to the requirements of the manufacturing process.
By default, sharp edges should be broken and deburred to prevent any risk of contamination or harm to people using the part. Edge condition affects accuracy and performance, meaning careful attention must be given when specifying edge condition during CNC machining operations.
Surface finish and tolerances go hand in hand, so it’s essential to have both dialed in for a project’s proper fit and function. For many projects, an as-machined finish (125 Ra or better) is sufficient, but additional finishing options can be specified depending on the needs of your project.
When getting a quote for CNC machining services, specify any surface finish requirements. Having this information, in the beginning will help ensure that your project outcome meets all your expectations.
china metal CNC machining
ETCN is a professional metal CNC machining supplier in China. We provide high-quality custom CNC machining services for customers all over the world. We have a team of experienced engineers and technicians who can handle any metal CNC machining project, from simple to complex. We also have a wide range of CNC machines that enable us to handle large-scale projects quickly and efficiently. If you need precision metal CNC machining services, please get in touch with us today. We would be happy to help you get the job done right.
CNC machining aluminum alloys is a highly accurate and efficient manufacturing process capable of producing complex parts and components with high precision and repeatability. These aluminum alloys are widely used in various industries due to their unique properties and characteristics, making them an ideal choice for many applications.
Aluminum 6061: This general-purpose alloy is known for its good strength-to-weight ratio, good corrosion resistance, and excellent machinability. It is commonly used in the aerospace, automotive, and construction industries.
Aluminum 5052: This alloy is known for its high strength, good formability, and excellent corrosion resistance, making it a popular choice for marine and transportation applications.
Aluminum 2024: This high-strength alloy is often used in the aerospace industry due to its good fatigue resistance and high strength-to-weight ratio. It is also known for its excellent machinability.
Aluminum 6063: This is a medium-strength alloy known for its good formability and corrosion resistance. It is commonly used in the construction industry for applications such as window frames and door frames.
Aluminum 7050: This high-strength alloy is known for its excellent fatigue resistance and high strength-to-weight ratio, making it a popular choice in the aerospace industry.
Aluminum 7075: This high-strength alloy is known for its excellent fatigue resistance and high strength-to-weight ratio. It is commonly used in the aerospace and defense industries.
Aluminum MIC-6: This high-strength, cast aluminum alloy is known for its excellent dimensional stability and flatness. It is often used in tooling and precision machining applications.
CNC machining copper
CNC machining copper uses computer numerical control (CNC) technology to shape and finish copper parts. This process involves using specialized CNC equipment, such as lathes, mills, and turning centers, to cut, drill, and mill copper into the desired shape or finish.
Copper 101 is a high-purity copper alloy with a minimum copper content of 99.9%. It is known for its high electrical and thermal conductivity, corrosion resistance, and good machinability. Copper 101 is commonly used in electrical and electronic applications and in the production of connectors, switches, and other electrical components.
Copper C110 is a high-conductivity copper alloy with a minimum copper content of 99.9%. It is known for its excellent electrical and thermal conductivity, as well as its corrosion resistance and good machinability. Copper C110 is commonly used in electrical and electronic applications and in the production of connectors, switches, and other electrical components. Copper C110 is also widely used in the aerospace and automotive industries due to its high strength and durability.
Both Copper 101 and Copper C110 are well-suited for CNC machining due to their excellent machinability and ability to hold tight tolerances. CNC machining allows for the precise and repeatable production of parts with excellent surface finishes, making it an ideal choice for producing high-quality copper parts.
CNC machining bronze
CNC machining allows for the precise and repeatable production of parts with excellent surface finishes, making it an ideal choice for producing high-quality bronze parts. Copper C932 is well-suited for CNC machining due to its excellent machinability and ability to hold tight tolerances.
Copper C932, also known as SAE 660 bearing bronze, is a high-strength bronze alloy that is commonly used in bearing and wear applications. It is made up of copper, tin, and zinc, with a minimum copper content of 88%. Copper C932 is known for its high strength, good corrosion resistance, and excellent machinability, making it well-suited for CNC machining.
In addition to its use in bearing and wear applications, Copper C932 is also commonly used in the production of gears, bushings, and other mechanical components. It is often used in the aerospace, automotive, and marine industries due to its high strength and durability.
CNC Machining Brass
CNC Machining Brass uses Computer Numerical Control (CNC) machines to shape and produce metal parts from brass materials. This process is particularly useful in producing highly intricate or complex parts that are difficult to make through traditional manufacturing methods. Brass, an alloy of copper and zinc, is a popular choice for CNC machining because it has several desirable characteristics, such as strength, corrosion resistance, and good electrical properties.
Copper 260 contains 60% copper and 40% zinc, while Copper 360 contains 90% copper and 10% zinc.
Due to its higher copper content, Copper 360 has superior strength, corrosion resistance, and electrical conductivity compared to Copper 260. This makes it an ideal choice for producing parts that require greater durability, such as valve stems and motor shafts.
In addition to their high strength and corrosion resistance, both types of brass have excellent machinability,, making them suitable for CNC machines. The combination of their strength with the precision of CNC machining makes them a popular choice for manufacturing components requiring tight tolerances or intricate shapes.
With the ability to create complex geometries quickly and accurately, CNC Machining Brass can help reduce costs when producing small batches or prototypes. As well as achieving high accuracy levels, this process also produces minimal waste material, so it can be more environmentally friendly than other methods of production when using recyclable materials like brass alloys.
CNC Machining Stainless Steel
CNC Machining Stainless Steel is a production process in which precision machining is performed using computer numerical control (CNC) equipment. CNC machining can create parts and components with highly precise dimensions and complex shapes out of many types of stainless steel.
Nitronic 60 (218 SS): This austenitic stainless steel offers excellent wear and corrosion resistance, making it suitable for use in harsh environments where other metals may not fare well. It also has high strength, toughness, and flexibility, enabling it to withstand extreme temperatures without cracking or warping.
Stainless Steel 15-5: This precipitation-hardening martensitic stainless steel features good corrosion resistance and high strength at elevated temperatures. It also has good formability and weldability, making it ideal for automotive parts and water pump applications.
Stainless Steel 17-4: This semi-austenitic precipitation-strengthening steel offers high strength, excellent corrosion resistance, and superior toughness in extreme temperatures. As such, it’s often used in aerospace, medical, and oil & gas applications that require robust materials that can withstand challenging conditions.
Stainless Steel 18-8: This austenitic chromium-nickel alloy is an inexpensive option commonly used for food preparation equipment due to its superior corrosion resistance. It also has moderate strength and good formability.
Stainless Steel 303: This free machining grade of stainless steel offers good corrosion resistance and high tensile strength for easy fabrication into various components. Additionally, its austenitic structure makes this material nonmagnetic but retains some magnetic permeability when cold worked.
Stainless Steel 316/316L: These austenitic alloys are widely used because they feature superior corrosion resistance over standard 304/304L grades, even in marine environments where they come into contact with saltwater regularly. They are highly resistant to pitting, crevice corrosion, and chloride stress cracking due to their higher molybdenum content compared to standard 304 grades.
Stainless Steel 416: As one of the most widely used free machining grades of stainless steel, this material features excellent machinability while maintaining good mechanical properties via heat treatment processes like hardening or tempering. This grade of stainless steel can be readily welded without relying on additional filler metal or any specialized preheating requirements, thanks to its low carbon content relative to other stainless alloys.
Stainless Steel 410: This basic martensitic grade of stainless steel offers exceptional hardness and moderate corrosion resistance depending on how it’s treated after fabrication; however, this grade should not be exposed to temperatures exceeding 350°F (177°C). Its excellent mechanical properties make it ideal for applications where strength is more important than aesthetics, such as fasteners or machine screws, rather than decorative components like jewelry or kitchen appliances.
Stainless Steel 420: Also known as “cutlery” grade stainless steel due to its exceptional hardness compared to most other ferrous materials available today; however, this comes at the expense of poor welding characteristics since it tends to hot cracking during post-weld heat treatment processes unless special precautions are taken before welding operations.
Stainless Steel 440C: As one of the hardest grades available today among all steels, including both ferrous and nonferrous varieties, this material displays exceptional wear resistance properties along with good corrosion protection, making it suitable for use in knife blades, medical instruments, bearings, and valve parts operating under corrosive conditions. Its low magnetic permeability allows it to perform well inside instruments requiring highly sensitive magnetic field measurements like MRI machines.
CNC machining steel
CNC machining steel is a process by which machines shape and form metal products. This process is often used in manufacturing components, tools, and other objects that require precision.
Steel 1018 is mild steel with low carbon content and good weldability properties. It has excellent machinability but is typically only suitable for applications that do not require high strength or wear resistance.
Steel 1215 is similar to steel 1018 but has a slightly higher carbon content. It also has good weldability characteristics and is more suitable for applications requiring increased strength or wear resistance than those requiring machinability. Steel 1215 also performs well under heat treatment conditions, making it popular in many industries, such as automotive and construction.
Steel 4130 is a chromium-molybdenum alloyed steel with good weldability properties and excellent heat treatment capabilities. It has excellent flexibility and toughness at high strength levels, which makes it ideal for structural parts such as gears, shafts, engine mounts, etc. It also provides excellent corrosion resistance when exposed to seawater or chloride environments.
Steel 4140 is another chromium-molybdenum alloyed steel with a slightly higher carbon content than 4130. It offers similar characteristics as 4130 but at higher hardness levels due to its higher carbon content, allowing it to be heat treated using oil quenching instead of air cooling methods like 4130 does. Steel 4140PH was an improved version of 4140 alloyed steel with even higher hardness levels when heat treated correctly than standard 4140 alloys can achieve. This makes it suitable for heavy-duty applications with greater wear resistance, such as mining equipment or agricultural machinery gears and shafts.
Steel 4340 is an ultra-high strength alloyed steel used in aerospace industry parts its superior tensile strength even at elevated temperatures compared to most other alloys available today. It also features excellent fatigue resistance allowing parts made from 4340 alloyed sheets of steel to retain their shape even after repeated cycles of usage over long periods without showing any signs of fatigue failure or cracking due to stress cycles applied during operation or service life cycle testing procedures applicable in aerospace industry standards today.
Last but not least, Steel A36 offers good weldability properties while providing decent overall strength levels across its range depending on the grade chosen by the user during its selection phase based on application-designed parameters. It can be found in various forms such as bars, plates, sheets, etc . which make it a popular choice for many industries, including automotive, marine, energy sectors, etc. Steel A36 load-bearing capacity increases when plate thickness increases,, making it a a popular choice among engineers who design structures with static loading conditions,, such as bridges, frames, buildings,, etc.
CNC machining titanium
CNC machining titanium is a process that uses Computer Numerical Control (CNC) to shape and form titanium into the desired product. The CNC machines precisely manipulate the cutting tools to create intricate shapes and patterns in the material. Titanium is an ideal material for CNC machining as it is strong, lightweight, and highly resistant to corrosion. It can be used for various applications in various industries, such as aerospace, medical, automotive, and sporting goods.
Titanium Grade 2 is one of the most commonly used grades of titanium for CNC machining. It has an excellent strength-to-weight ratio, low modulus of elasticity, and high corrosion resistance, making it an ideal choice for many engineering applications. This grade also offers superior weldability, impact toughness, and ductility, which lend well to parts or components with complex features or tight tolerances. Common applications include aircraft components, medical implants, golf clubs, and other sporting goods.
Titanium Grade 5 offers a higher strength than Grade 2 with comparable weight-saving benefits. It has excellent corrosion resistance making it suitable for use in extremely corrosive environments such as marine or coastal settings. It also exhibits very good fatigue strength, which is beneficial when designing components that will endure cyclic loading over time. Common applications of this grade include aerospace fasteners, marine fittings, chemical processing equipment, and motorsport components due to their superior strength and lightweight properties.
CNC machining zinc
CNC machining zinc is a process used to fabricate complex and intricate parts with precision. Zinc alloys are a particular type of metal that can be machined by this process, specifically through Computer Numerical Control (CNC) machines. The CNC machining process for zinc provides manufacturers with an efficient and cost-effective way to produce high-quality components from the alloy.
Zinc alloys have several important characteristics that make them suitable for CNC machining. Firstly, zinc has excellent dimensional stability, allowing parts produced from it to be consistent in size and shape over time. This means that the part will remain dimensionally accurate even after repeated use or exposure to extreme temperatures. Additionally, zinc alloys also have a high level of corrosion resistance due to their protective surface layer, which resists the damages caused by oxidation. This increases the durability and lifespan of components made from zinc alloys.
Furthermore, zinc alloys are relatively easy to machine compared to other harder metals, such as steel or aluminum, due to their softer nature and low melting point. This property makes them ideal for more complex designs, as they can easily be formed into intricate shapes without sacrificing precision or quality. As a result, components made from zinc alloy are often lighter yet stronger than those made from other metals and, therefore, capable of performing at higher levels while being more cost-effective.
Overall, CNC machining zinc is an effective method for producing high-quality components from this alloy due to its dimensional stability and corrosion resistance and its easier formability compared to other metals.
Plastic CNC Machining China
ETCN offers precision plastic CNC machining services to help you with all your product needs. We have a wide range of equipment and expertise to handle even the most complex projects. With our high-quality CNC machines, we can provide fast and accurate results for your products. Contact us today to discuss your project!
CNC machining abs
CNC machining ABS (acrylonitrile butadiene styrene) is a thermoplastic offering excellent rigidity and dimensional stability. It has a good balance of properties such as strength, stiffness, hardness, impact resistance, and heat resistance, making it the material of choice for many applications. CNC machining ABS is often used to produce parts such as automotive components, medical devices, industrial machinery parts, and consumer products.
ABS is an amorphous polymer that can be processed in numerous ways, including injection molding, extrusion, and thermoforming. The thermoplastic also offers excellent formability and chemical resistance, making it ideal for applications requiring high wear-resistance or corrosive environments. Its good electrical properties make it an ideal choice for electronic components, while its toughness makes it suitable for industrial uses. Its low water absorption rate makes it suitable for outdoor use, withstanding temperature extremes of up to 90°C.
CNC machining ABS is a cost-effective solution since it can be easily formed into complex shapes with precision accuracy in larger volumes than other materials such as metals or ceramics. The material also offers good surface finish quality allowing for better aesthetics when necessary. With its easy machineability, CNC machining ABS allows for tight tolerance requirements, often needed to produce components requiring close fits in assembly operations.
In terms of its physical characteristics, CNC machining ABS provides excellent mechanical strength and rigidity, making it the ideal choice for applications requiring high impact resistance or weight-bearing capacity, such as exterior automotive panels.
Additionally, the material has good thermal stability,, making it resistant to sudden changes in temperature without adversely affecting its structural integrity. Furthermore, CNC-machined ABS exhibits superior flame retardance making it suitable for safety-critical applications like aircraft interiors or electrical components.
CNC Machining Acrylic
With the right tooling and setup, CNC Machining Acrylic can efficiently produce high-quality parts with extremely tight tolerances in mass-production quantities. The process can also produce finished pieces with low-stress levels, ensuring that parts remain strong even after machining.
Due to its strength, clarity, lightweight, and chemical resistance. It has excellent weathering and UV stability, making it suitable for outdoor applications.
Acrylic can also be easily machined and molded into various shapes and sizes. Its high optical clarity makes it ideal for signage, displays, and other visual products, while its ability to be formed into complex shapes lends itself well to intricate machinery components. It can be machined with conventional metalworking equipment, including lathes, milling machines, drill presses, and routers.
By using CNC machining for fabrication projects involving acrylic material, you can achieve highly accurate results relatively quickly compared to other processes, such as laser or waterjet cutting or thermoforming.
CNC Machining Delrin
CNC Machining Delrin is a process of cutting, shaping, drilling, and finishing components out of Delrin plastic, a thermoplastic material made from polymerized formaldehyde. This machining technique allows for producing extremely specific components with excellent repeatability and accuracy and complex shapes that are impossible with traditional manufacturing methods.
It has high tensile strength, low coefficient of friction, and good chemical resistance. It can also withstand high temperatures without deformation, making it suited for more than just prototyping applications. Additionally, the material’s excellent dimensional stability ensures consistent manufacturing results.
Due to its superior wear and abrasion resistance, the material is often used to create gears, connectors, and other mechanical parts. Its ability to be machined into complex shapes makes it suitable for producing decorative components. Furthermore, Delrin exhibits great electrical insulating properties, making it ideal for electrical and electronic components such as circuit breakers and other protective enclosures.
Compared to metals such as aluminum or steel, Delrin offers several advantages when it comes to production costs; since the material does not require annealing after machining, nor secondary surface treatments or painting operations like metals do to achieve desired finishes or color changes. Delrin is ideal for cost-effective production runs or short-run orders involving intricate shapes or small batch sizes.
garolite g10
CNC Machining Garolite G10 is a type of composite material specifically designed for machining applications. It comprises layers of fiberglass cloth and phenolic resin, which are sandwiched together to form a hard yet flexible material. This material is generally used to construct parts in industrial machinery and create components such as gears, bearings, and other mechanical parts.
Firstly, it has excellent thermal properties and can withstand high temperatures without significant damage or distortion. Secondly, it has very good electrical insulation properties, making it suitable for electrical components such as switches and relays. Thirdly, its wear resistance is excellent; its extremely low coefficient of friction makes it ideal for use in high-speed motion applications where wear resistance is critical. Moreover, this material boasts a tremendous strength-to-weight ratio – making it perfect for manufacturing lightweight but tough parts. Lastly, Garolite G10 has excellent dimensional stability; even after repeated heating and cooling cycles,, this material will return to its original shape with minimal distortion.
Garolite G10 also comes in various forms depending on what application you need – ranging from molded shapes to sheets and rods that can be cut into custom shapes using CNC tools. Furthermore, this versatile product can be easily machined using many cutting tools, such as end mills, drills, routers, and saws – allowing you to quickly and efficiently create highly precise parts with tight tolerances quickly and efficiently.
All these factors combine to make CNC Machining Garolite G10 an ideal choice for all kinds of machining needs – from small intricate items like electronic components to large-scale pieces such as gears or structural supports. Its combination of durability, flexibility, strength, and dimensional stability make this product an outstanding option for various of projects in many industries around the world – ensuring reliable performance at an economical price point!
CNC Machining Hdpe
CNC Machining Hdpe is a process that involves the use of computer-controlled machines to shape and cut various materials, including High-Density Polyethylene (HDPE). HDPE is a thermoplastic material that has become increasingly popular in many industries due to its superior physical properties.
It is a lightweight, corrosion-resistant material with excellent chemical resistance and low moisture absorption. It has excellent weatherability and can be used in outdoor applications without fear of fading or discoloration. The additional advantages of HDPE include high impact strength, low cost of production, good electrical insulation properties, high dimensional stability, and low thermal conductivity.
Manufacturing parts from HDPE requires precision cutting and shaping through CNC machining processes such as milling, drilling, turning, routing, and grinding. This enables the production of components with complex geometries at highly accurate tolerances for industrial applications ranging from automotive components to medical implants. Milling HDPE allows the controlled removal of material to produce specific shapes with tight tolerances. In contrast, drilling allows for holes in any desired location within the part. Turning processes create components such as gears with cylindrical features while routing processes allow for the creation of slots or channels on a part’s surface. If required, grinding may also achieve extremely fine surface finishes on HDPE components.
Overall, CNC Machining HDPE provides manufacturers with an efficient and accurate way to produce parts with superior physical characteristics compared to other materials at lower costs. Its wide range of physical properties makes it suitable for numerous applications across various industries worldwide.
nylon machining
CNC Machining Nylon is a method of cutting and carving parts from nylon materials using Computer Numerical Control (CNC) machines. This process involves programming the CNC machine to cut or carve out a particular piece based on instructions given by a computer.
Nylon is an incredibly versatile material that can be used for many applications. It has good mechanical properties, high tensile strength, flexibility, and resistance to wear and tear. Its low friction coefficient makes it ideal for precision machining applications such as the automotive industry or medical device components.
Additionally, it is resistant to chemicals and can withstand harsh environmental conditions such as extreme temperatures and high levels of ultraviolet radiation. It also has excellent thermal conductivity properties, allowing heat dissipation while maintaining its structural integrity.
Furthermore, it features superior electrical insulation properties, making it unique among engineering plastics and suitable for electrical devices like connectors, transformers, and other components with higher voltage requirements. Nylon is also recyclable, enhancing its sustainability credentials and making it more attractive to manufacturers looking for greener alternatives in their production processes.
CNC machining polycarbonate
CNC machining polycarbonate is a process that involves using computer numerical control (CNC) equipment to mill, drill, cut, and shape components from Polycarbonate thermoplastic material.
Polycarbonates are a class of strong and lightweight engineering plastics known for their durability and heat resistance. They also have excellent optical clarity, chemical resistance, and flame retardancy, making them ideal for many applications requiring high-performance materials.
Polycarbonate is an extremely versatile material used in various industries ranging from medical equipment to automotive components to consumer products. Its strength makes it suitable for applications where impact resistance is important,
In contrast, its light weight makes it ideal for applications where weight is an issue, such as aerospace or robotics. Additionally, the material’s low shrink rate allows it to maintain dimensional stability even under high temperatures, making it suitable for demanding applications such as food processing or electrical insulation.
Polycarbonates also boast extremely high moisture resistance,, allowing them to withstand harsh environments without degrading or rusting over time. Overall, these attributes make polycarbonate ideal for various industrial applications requiring superior performance without sacrificing aesthetics or safety.
peek CNC machining
Peek CNC machining is a form of machining that utilizes Computer Numerical Control (CNC) to create components from PEEK (Polyether Ether Ketone).
PEEK is an engineering thermoplastic renowned for its strength and durability, making it one of the most popular materials in CNC machining. It has excellent chemical resistance, good electrical properties, low flammability, and high flexural strength. Due to these characteristics, PEEK is often used in the medical sector, aerospace industry, automotive industry, and other demanding applications.
PEEK CNC machining offers manufacturers several advantages. These include improved accuracy and repeatability compared to manual machining processes; reduced lead times due to faster production; decreased overhead costs; and improved product quality thanks to greater precision, reduced variation, and fewer errors. Additionally, CNC machines can be programmed with custom cutting paths or automated with CAM software, so they’re highly versatile. They can make complex parts that would otherwise require manual labor or multiple tool changes.
From a mechanical standpoint, PEEK is extremely robust: it’s strong enough for use in high-stress environments such as aerospace or automotive components (where metals may fail). It has a melting point of 343 °C (650 °F), which makes it resistant to extreme temperatures; keeps its shape up to 100°C (212°F); boasts a high tensile strength of 12 MPa (1750 psi); can withstand pressures up to 10 MPa (1450 psi); and exhibits good creep resistance even at elevated temperatures.
Due to its high stiffness-to-weight ratio—which is about 40% higher than many metals—PEEK also provides excellent vibravibration-dampeningbilities. This makes it especially useful for items such as electronics enclosures or data storage drive housings where physical shock needs to be minimized. It’s also self-lubricating because of its low surface adhesion properties; moving parts don’t require additional lubricants or coatings as some metals do.
Overall, PEEK CNC machining provides small-batch manufacturers with an efficient solution for producing complex parts quickly and accurately without sacrificing quality or durability. By utilizing CNC machinery and specialized cuands designed specifically for the material being processed—such as carbide end mills specifically designed for machining plastics—manufacturers can consistently produce canthat meet their exact specifications while optimizing their bottom line.
CNC machining polypropylene
CNC machining polypropylene is a process of cutting, drilling, or milling materials with precision and accuracy. Polypropylene is one of the most commonly used thermoplastics in manufacturing due to its cost-effectiveness, ease of shaping, and overall low weight.
It has excellent chemical resistance, strength, and high impact resistance up to 140°F (60°C), making it suitable for many applications such as automotive components, medical devices, and packaging. Additionally, polypropylene has good thermal stability and electrical insulating properties. It can also withstand a wide range of temperatures from -4°F (-20°C) to 212°F (100°C).
Polypropylene is available in two main forms: homopolymers and copolymers. Homopolymers are more durable than copolymers, but their impact strength is lower. Copolymer grades are generally tougher than homopolymers and better at maintaining flexibility at low temperatures. Polypropylene can also be reinforced with glass fibers to improve its rigidity, strength, and stiffness without increasing its density significantly.
When CNC machining polypropylene, it is important to consider the material’s behavior under various temperatures and its reactivity with cutting tools. The material’s flexibility changes when exposed to heat generated by the machining process, makingrrs prominent on the workpiece surface after finishing operations have been completed if not managed properly. As an example of this challenge, certain tool geometries, such as diamond-coated carbide drills, should be used to minimize burring issues when CNC machining polypropylene parts. Furthermore, specific cutting speeds must be considered for good surface finish results to be achieved on the machined part’s surface, with minimal effort spent on secondary operations like deburring or polishing afterward.
CNC machining ptfe (teflon)
CNC machining PTFE, or polytetrafluoroethylene (PTFE), is a strong, lightweight, and durable engineering material with a wide range of applications.
The material has excellent thermal and chemical resistance, low coefficient of friction, and electrical insulation properties. It is often used to make gaskets, seals, tubing, and bearings because of its ability to resist temperature extremes from -360°F to 500°F (-200°C to 260°C). PTFE is also used in many industrial applications such as oil seals, chemical processing equipment, robotics components, and automotive parts due to its high strength and chemical resistance.
PTFE is an inert material with excellent dielectric properties. It does not react with water, acids, or bases and is highly resistant to most solvents. Its low coefficient of friction makes it ideal for medical instruments such as stethoscopes and surgical tools. PTFE can also self-lubricate, making it for use in bearings and other moving parts that need a long service life without needing frequent lubrication changes.
In terms of CNC machining PTFE (Teflon), this synthetic polymer can be formed into complex shapes with tight tolerances by utilizing Computer Numerically Controlled (CNC) machines. These machines use specially designed computer programs written in G-code language that is programmed into the machine’s control system. This program tells the machine how to move its cutting tools so that all of the parts created meet exact specifications according to customer drawings or blueprints. Various types of cutting tools from different materials may be used depending on the shape being machined, such as end mills made from high-speed steel or carbide cutters for more intricate shapes. In addition, coolants like water-soluble oils are often used while CNC machining PTFE (Teflon) to reduce heat build-up and improve the finish quality of the machined part.
PTFE’s combination of superb mechanical properties and its excellent thermal stability makes it an ideal choice for precision CNC machining applications where accuracy is paramount. As such, many companies rely on CNC-machined PTFE components for their industrial needs because they can count on being both reliable and durable over time with minimal maintenance requirements due to their impressive self-lubricating capability.
machining UHMW
CNC machining UHMW (ultra-high molecular weight polyethylene) is an advanced manufacturing process that uses computer numerical control to shape, cut, and drill UHMW components. The CNC process allows for extremely precise machining of UHMW shapes and components with high accuracy. This is especially beneficial when manufacturing complex parts that require tight tolerances or intricate detailing.
UHMW is an incredibly strong and durable thermoplastic with excellent properties, including low friction, weather resistance, wear resistance, and chemical resistance. Its high tensile strength makes it ideal for applications where durability and strength are essential. UHMW also has excellent compression strength, making it suitable for shock-absorbing materials in protective equipment or interior automotive parts such as door panels and dashboards. UHMW has a low friction coefficient, making it useful for applications like conveyor belts, rollers, and bearings that need to reduce abrasion while in motion.
The machinability of UHMW is one of its greatest qualities. It can be cut into various shapes using conventional tools or CNC machines with great accuracy and precision due to its low coefficient of thermal expansion. The material can be machined using multiple techniques, including drilling, turning, milling, forming, punching, sawing, lapping/polishing, and grinding, The right tooling and setup can also be tapped into holes for a secure fitment where necessary.
When performing CNC machining on UHMW, there are key considerations to keep in mind to achieve the desired results without damaging the material or the cutting tools themselves. Firstly the cutting speed should be kept relatively low compared to other materials since higher speeds lead to shorter tool life due to increased heat generation, which can cause warping or melting of the material if prolonged exposure occurs at these speeds. Additionally, because of its slick surface finish lubrication should always be used when machining UHMW to reduce friction between the cutting tool and the material being worked on while also reducing built-up heat created by working on the component itself over time. Finally, selecting the proper cutting tool is important when working with this material as duller tools will cause excessive wear on both sides, leading to poor surface finishes and premature failure more quickly than sharper tools would provide better results overall when dealing with this unique plastic material type.
CNC PVC
CNC machining PVC fabricates or constructs components using Computer Numerical Controlled (CNC) machines. It involves manipulating computer-controlled cutting tools to shape the material into various shapes and sizes according to predetermined specifications.
CNC machining PVC is a process of fabricating or constructing components with the use of Computer Numerical Controlled (CNC) machines. It involves the manipulation of computer-controlled cutting tools to shape the material into various shapes and sizes according to predetermined specifications. CNC machining is one of the most common processes used to produce prototypes and finished parts quickly and accurately.
PVC, or polyvinyl chloride, is a type of thermoplastic that is an excellent candidate for CNC machining due to its durability, strength, and ease of machinability. Its rigid nature allows for intricate parts to be produced without sacrificing structural integrity, making it ideal for applications that require structural strength such as connectors, fittings, and fixtures. Additionally, PVC can withstand extreme temperatures and it is highly resistant to corrosion, making it suitable for environments that require protection from harsh conditions. Furthermore, its economical cost makes it more economical than other materials in some applications.
In terms of machinability, PVC has low thermal conductivity which helps reduce tool wear by keeping heat away from cutting edges. Because of this feature as well as its low friction coefficient, it provides an efficient cut with minimal stress on tools when compared with other materials such as aluminum or stainless steel. The low friction also helps minimize surface finish issues while enabling tight tolerances on intricate parts. Furthermore, when machined correctly with proper methods and tooling selection coupled with strategic programming approaches like helical interpolation and slow feed rates – both critical elements in achieving great results – PVC can provide excellent surface finishes that often surpass those achievable with other materials.
The combination of these features makes PVC an ideal material choice for CNC machining applications where strength and long-term performance are key factors in determining success. As a result, it has been used in a variety of industries ranging from consumer products to aerospace engineering due to its ability to hold up under extreme conditions while providing reliable performance at a lower cost than alternative materials like aluminum or stainless steel.
CNC machining parts china
ETCN is a professional manufacturer of CNC machining parts with over 10 years of experience in the industry. We use the latest technology and equipment to produce high-quality parts that meet your specifications. Our team of experts will work with you to create a part that meets your needs and exceeds your expectations. Contact us today to get started!
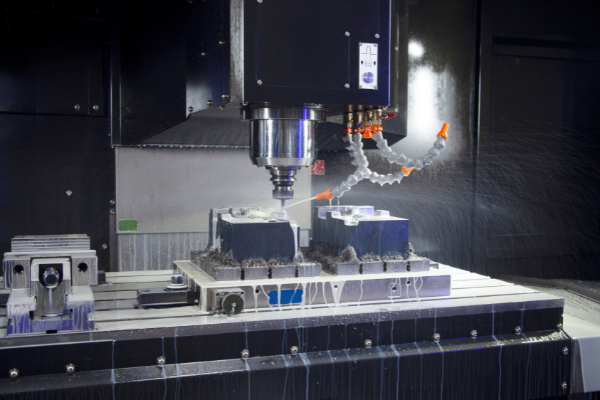
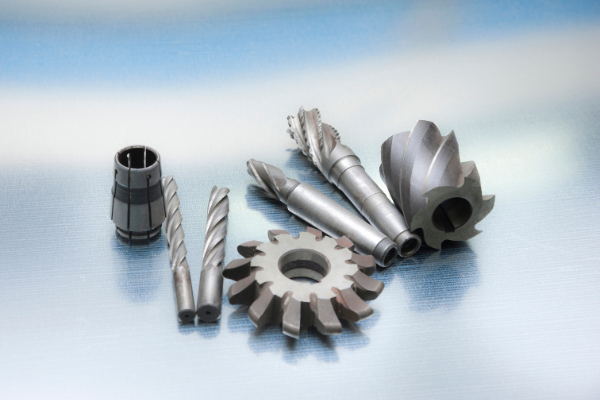
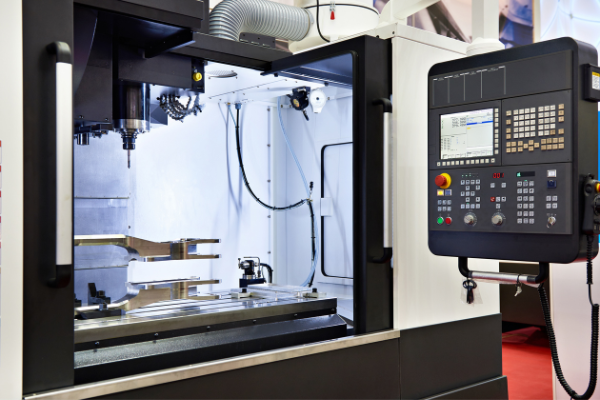
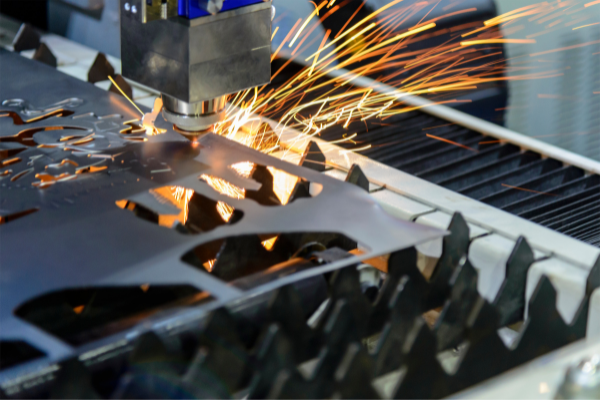
china cnc machining parts manufacturer
Cnc Machining Parts China
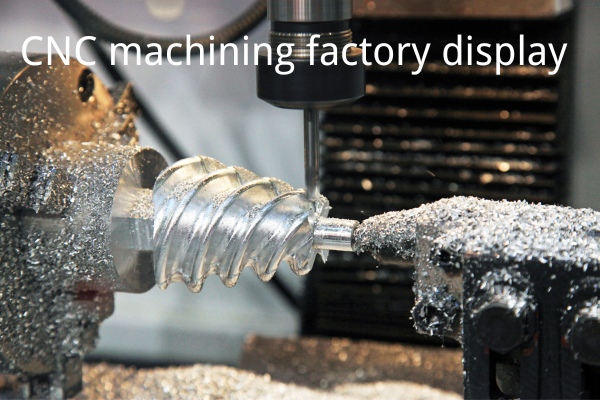
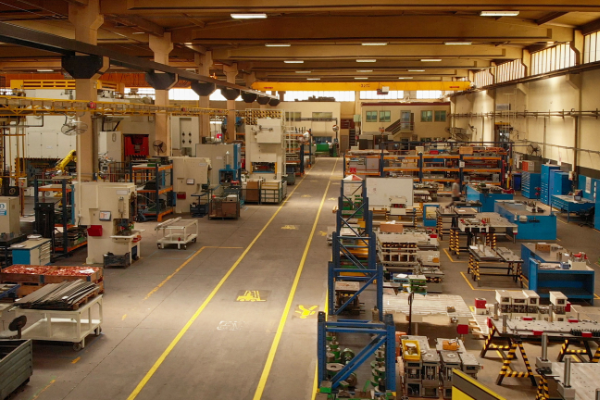
Benefits of investing in Chinese CNC machining parts
2. Reduced Downtime:
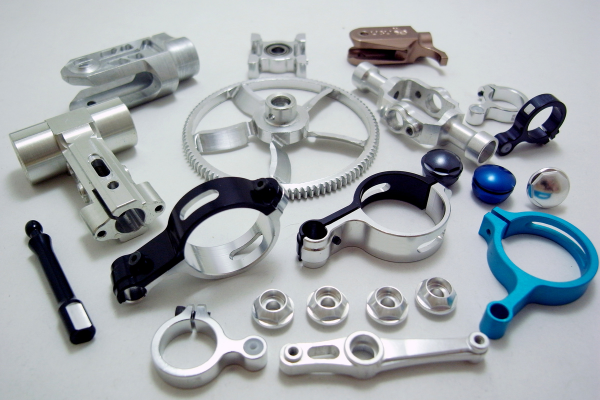
Benefits of investing in Chinese CNC machining parts
3.Cheaper overall cost
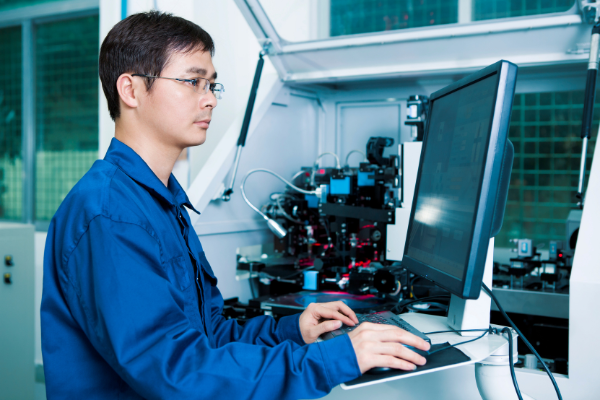
CNC Machining Surface Finish
CNC Machining surface finish results from machining processes such as grinding, honing, and polishing. It measures how smooth and even the surface of a material is after it has been cut or ground by a machine tool. The type of finish required depends on the application and the desired visual effect. Generally, the smoother the finish, the higher the quality and performance. Depending on the operation performed and the machining materials, various surface finishes are available.
Standard (As-Milled) is a smooth, relatively flat surface with minimal imperfections. The standard finish should have a proper and consistent shape with no visible blemishes or marks.
It should also be free of burrs and sharp edges that could cause wear or damage to components during assembly. It is important to note that the quality of the machined surface depends on the specific CNC machining parameters utilized by the manufacturer.
Tumbled is a slightly rougher finish created by tumbling the part in an abrasive media.
This type of finish is often used to achieve a uniform surface appearance and improved gripping surfaces on complex parts. It can also create a soft, matte finish on softer materials like aluminum or polymer.
The result is a two-dimensional, textured finish with no visible flaws or blemishes.
The industry standard parameters of Titanium anodizing include temperature, current density, anode-to-cathode distance, and time.
The temperature range for Titanium anodizing is between 40°F–90°F (4°C–32°C). The current density should not exceed 2 amps/square inch. The anode-to-cathode distance should be between
0.5” and 3” (1cm and 7.6 cm).
The time for the process should be between 8 to 10 minutes at the standard parameters.
The industry standard parameters of Chem Film (Chromate Conversion Coating) include the metal surface preparation, temperature, pH, immersion time, and post-treatment.
The metal surface should be free from foreign particles or debris before application. The ideal temperature range for Chem Film is between 78°F–86°F (25°C–30°C).
The pH levels should be maintained between 3-5.5 by adjusting the concentration of the chemical solution used in the process. The amount of time for immersion depends on the desired thickness of the coating but usually ranges from 12-15 minutes. Post-treatment may include air drying or baking for superior durability.
The industry standard parameters of Powder Coat include pre-treatment, powder mix, temperature, airflow, and curing.
The pre-treatment step ensures superior coating adhesion and should include degreasing and surface preparation.
The powder mixture should be between 80-90% by weight, with several sorts available depending on the desired finish. The temperature of the application should be between 325°F–425°F (163°C–218°C). A low to medium air pressure should be used to achieve even coverage across the material being coated.
Finally, curing requires post-treatment with heat to achieve optimal performance, such as no chipping or fading.
The industry standard parameters of Electroless Nickel Plating include chemical pre-treatment, temperature, pH, time, and post-treatment.
The chemical pre-treatment is important to ensure proper adhesion and should involve a degreasing process using acids or alkalies. The ideal temperature range for the plating solution is between 90°F–110°F (32°C–43°C). The pH should be between 6.2-7.0 for optimal results.
Time for immersion varies but can generally range from 10-30 minutes depending on the desired thickness and composition of the material being plated. Post-treatment includes a warm water rinse followed by drying or an air blast to remove any remaining residue on the part’s surface.
The industry standard parameters of Gold Plating include pre-treatment, acid bath, temperature range, and current density.
The pre-treatment is important to ensure good adhesion and should involve a degreasing process with acids or alkalies, as well as some mechanical preparation, such as grinding or polishing, depending on the material being plated.
The acid bath should have an optimal pH between 1–2, while the temperature of the solution should be within the range of 70°F–90°F (21°C–32°C). Lastly, a low current density of 0.1–0.5 Amps/sq.in is typically used for the gold plating to achieve superior results.
The industry standard parameters of Zinc Plating include pre-treatment, temperature range, pH, and current density.
The pre-treatment is important to ensure good adhesion and should involve a degreasing process with acids or alkalies, as well as some mechanical preparation, such as grinding or polishing, depending on the material being plated. The optimal temperature range for the plating solution is between 70°F–90°F (21°C–32°C). The pH of the solution should be between 4–6 for best results.
Lastly, a low current density of 0.1–0.5 Amps/sq.in is typically used for zinc plating in order to achieve superior results.
The industry standard parameters of Silver Plating include pre-treatment, temperature range, pH, and current density.
The pre-treatment is important to ensure good adhesion and should involve a degreasing process with acids or alkalies, as well as some mechanical preparation, such as grinding or polishing, depending on the material being plated.
The optimal temperature range for the plating solution is between 70°F–90°F (21°C–32°C). The pH of the solution should be between 4–6 for best results.
Lastly, a low current density of 0.1–0.5 Amps/sq.in is typically used for silver plating to achieve superior results.
The industry standard parameters of Electropolishing for CNC machining include pre-treatment, temperature range, pH, current density, and time.
The pre-treatment is important to ensure good adhesion and should involve a degreasing process with acids or alkalies and an electrolytic clean for removing the scale. The optimal pH of the solution should be between 2–3 for best results. A low current density of 0.5–1 Amps/sq.in should be used to achieve superior electropolishing results.
The time needed depends on the material being electropolished and typically ranges from 5 seconds to several minutes. Finally, the optimal temperature range for the plating solution is between 70°F–90°F (21°C–32°C).
The industry standard parameters of Passivation for CNC machining include pre-treatment, temperature range, pH, current density, and time. The pre-treatment is important to ensure good adhesion and should involve a descaling process with acids or alkalies and an electrochemical clean to remove any oxides or residues from prior processes.
The optimal pH of the solution should be between 4–6 to achieve optimal passivating results. A low current density of 0.5–1 Amps/sq.in is typically used for passivation. Depending on the material being passivated, the time needed can range from 5 seconds to several minutes.
Finally, the optimal temperature range for the plating solution is between 70°F–90°F (21°C–32°C).
The industry standard parameters of PTFE Impregnated Hard Anodize for CNC machining include pre-treatment, temperature range, pH, current density, and time.
The pre-treatment is important to ensure good adhesion and should involve a descaling process with acids or alkalies and an electrochemical clean to remove any oxides or residues from prior processes.
The optimal pH of the solution should be between 3.5 and 4.5 to achieve superior PTFE impregnation results. A low current density of 0.3–0.6 Amps/sq.in is typically used for anodization. Depending on the anodized material, the time needed can range from 5 minutes to several hours.
Finally, the optimal temperature range for the plating solution is between 75°F–90°F (24°C–32°C).
The industry standard parameters of Anodized (Type II Or Type III) for CNC machining include pre-treatment, temperature range, current density, and time.
The pre-treatment is important to ensure good adhesion and should involve a descaling process with acids or alkalies and an electrochemical clean to remove any oxides or residues from prior processes. A low current density of 2–4 Amps/sq.in is typically used for anodization, with higher levels for thicker coatings. Depending on the anodized material, the time needed can range from 10 minutes to several hours.
Finally, the optimal temperature range for the plating solution is between 68°F–93°F (20°C–34°C).
The industry standard parameters of Bead Blast for CNC machining include abrasive type, air blast pressure, and nozzle size.
For successful bead blasting, selecting suitable abrasive media is essential. Many materials are available, such as steel shot, stainless-steel shot/grits, aluminum oxide/grits, walnut shell grit, and glass beads. The air blast pressure should be set according to the material being blasted and can range from 30–90 PSI.
Additionally, selecting a correctly sized nozzle is also important. The optimal nozzle size is determined by the surface area to be blasted and typically ranges from 1/16”–1”.
CNC Machining Design Guidelines
CNC machining design guidelines refer to the specific rules and methods that should be followed when designing components for CNC machining. These guidelines cover a range of topics, such as selecting the right materials for a particular application, choosing an appropriate level of complexity for features and designs, understanding toolpath optimization, familiarizing oneself with basic machine controls, and paying attention to proper tolerances. Following these guidelines is essential to creating successful parts suitable for CNC machining.
The industry-recommended standard for tapped/threaded hole depth in CNC machining is to achieve a minimum of two full threads into the component, with a maximum engagement of three full threads.
It’s also important to factor in tolerance requirements depending on the application, as this will ensure that the tapped/threaded holes can securely hold the parts.
Additionally, it’s important to choose a thread size and pitch that allows for easy installation of bolt and screw heads without compromising strength or stability.
The industry-recommended standard for undercuts in CNC machining is to achieve a depth of at least two times the thread’s major diameter, with a minimum of 0.006 inches.
Undercutting helps ensure proper thread engagement between internal and external components and provides an accurate fit. Additionally, it’s important to factor in clearance requirements for angled and blind holes, as this will eliminate the risk of interference during installation or assembly.
The industry-recommended standard for floor fillets in CNC machining is to achieve a minimum radius of 0.006 inches or greater.
Floor fillets help prevent stress concentrations in internal components and reduce the risk of binding components and causing premature failure due to fatigue.
Additionally, it’s important to consider other material type factors, such as strength and stiffness, for more advanced applications.
The industry-recommended standard for internal corner fillets in CNC machining is to achieve a minimum radius of 0.006 inches or greater, depending on the material type involved.
Internal corner fillets help to reduce stress concentrations within components, improve fatigue life and performance, and provide an aesthetically pleasing finish.
Additionally, it’s important to factor in other factors, such as size and strength requirements, when designing more complex components.
The industry-recommended standard for complexity in CNC machining is to use the guidelines provided by the chosen CAM software and to factor in other elements such as process optimization, tool selection, and feature detection when designing components.
Complexity should be tailored to the application to achieve desired results while minimizing any compromises that may arise with more intricate designs. Additionally, it’s important to consider machine capabilities when designing more advanced geometries.
precision cNC machining services
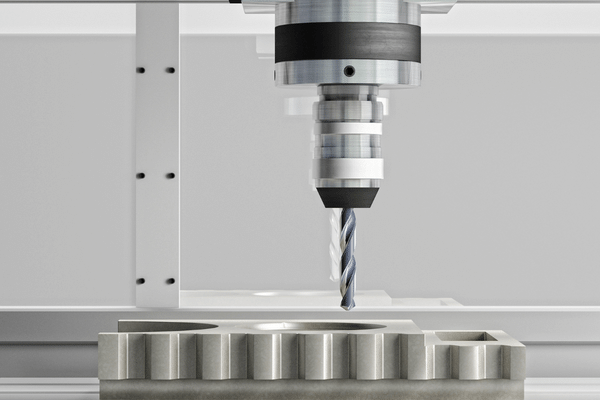
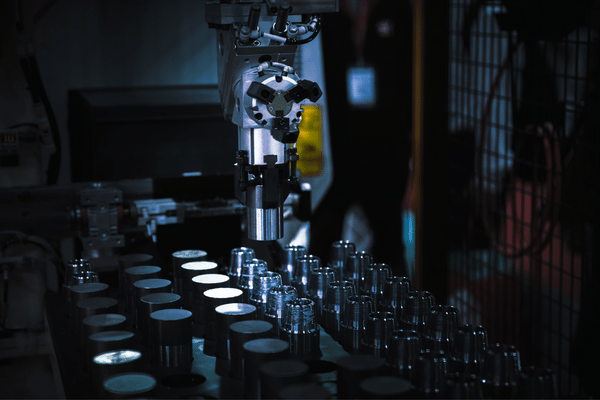
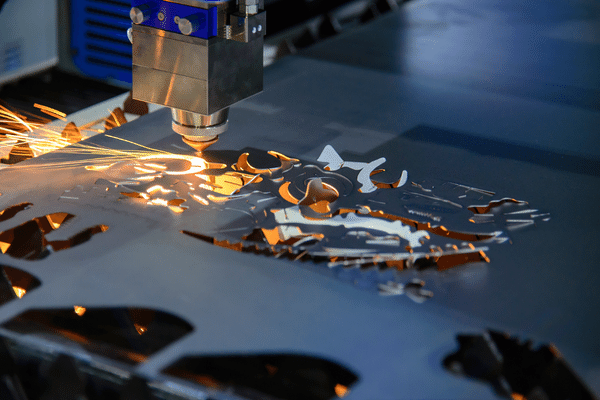
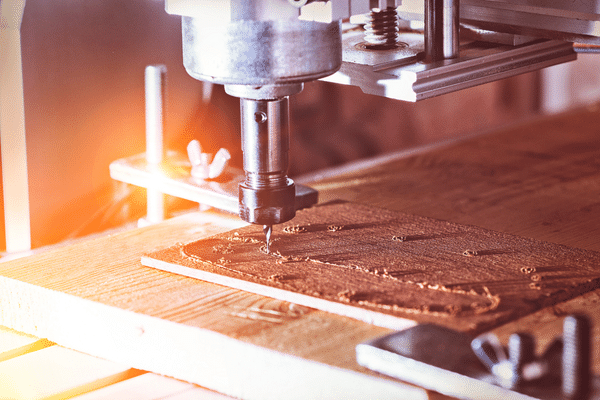
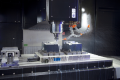
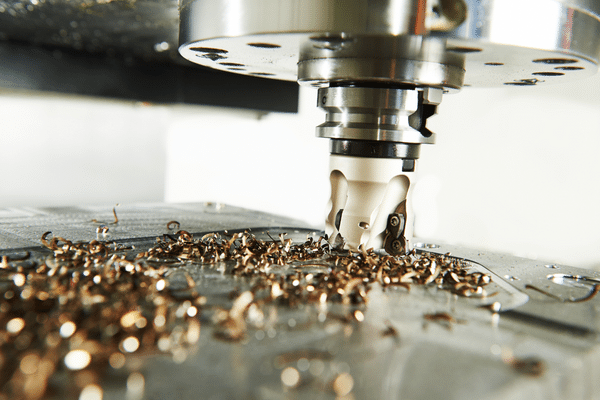
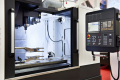
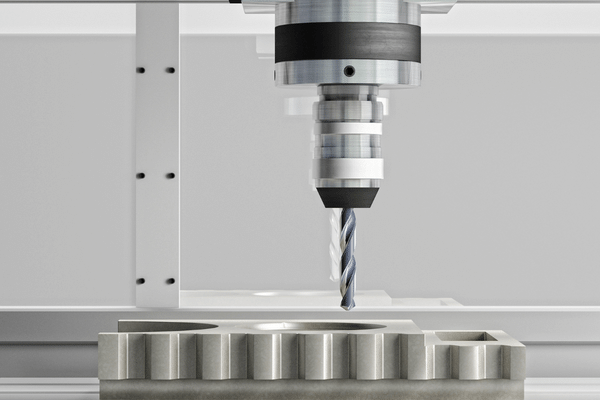
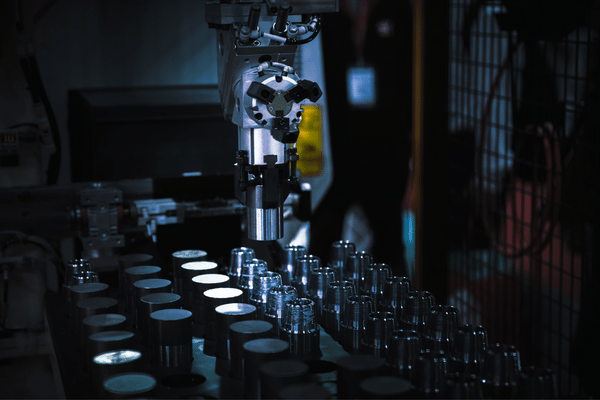
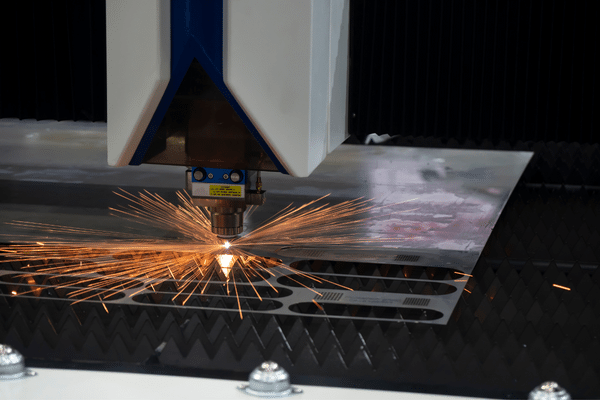
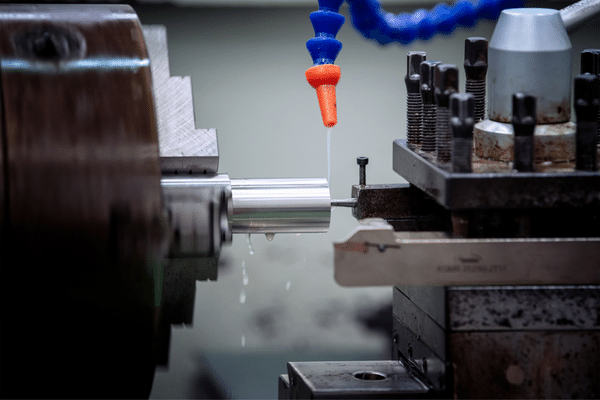
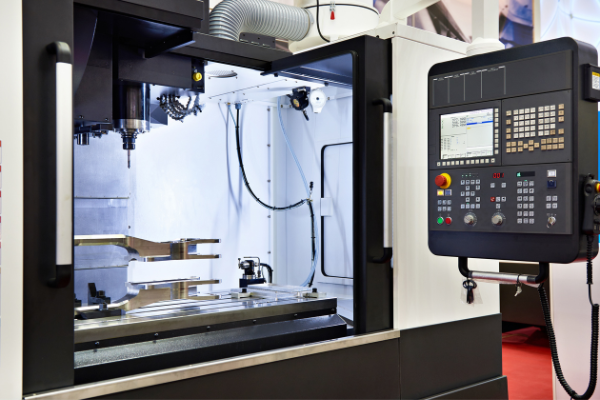

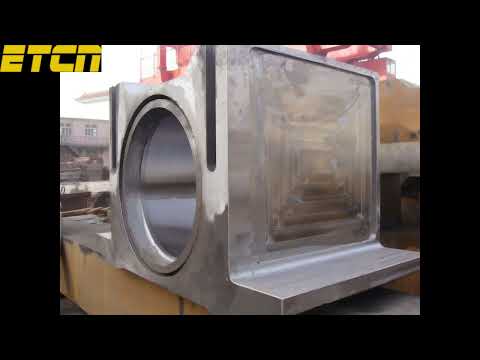
View Some Examples of Our Precision CNC Machined Parts
Latest Articles About CNC Machining Services
General Design Recommendations For Machined Parts
Many customers have questions concerning general design recommendations for machined parts to the machine because no one has given them some answers to their questions before.
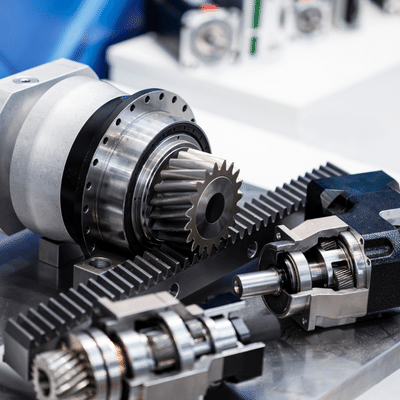
How CNC Designing Can Make Your Company More Profitable
Most CNC business owners are trying to gain more profits for their businesses.
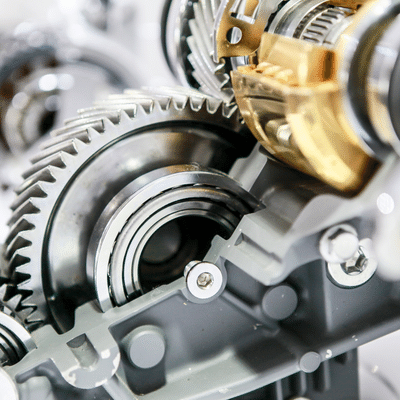
General Design Rules For Machining
In the following post, we will review the general design rules for machining. These are fairly basic rules, and you will have a better chance of success once you know them.
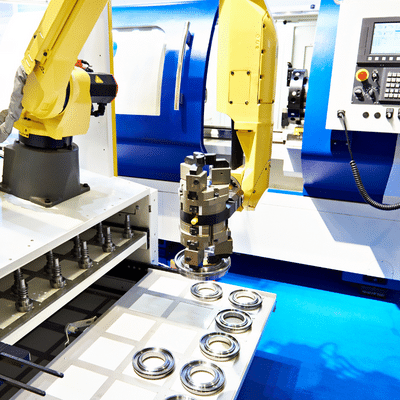
What Are CNC Machining Best Practices?
When setting up a CNC machining center, there are many best practices you need to follow. If you don’t, you could damage the machine or tooling, hurt yourself and others, or negatively impact your production rates.
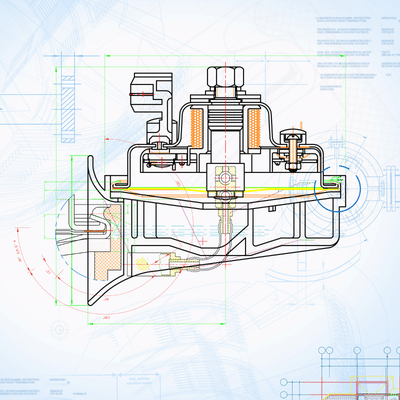
Design Guidelines For Machining
Machining is the most flexible of all the manufacturing processes. There are lots of designs that could be manufactured by machining. Product complexity, size, accuracy, and material properties usually influence the machining process selection.
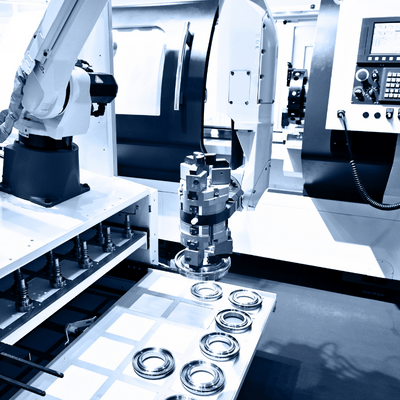
How To Design Parts For CNC Machining?
Here at ETCN, we provide machine shops with a huge selection of metals and machine parts designed for CNC machining. If you are new to CNC machining, or you’re simply looking for better ways to design your parts than you have in the past, I’ve got some useful information for you.
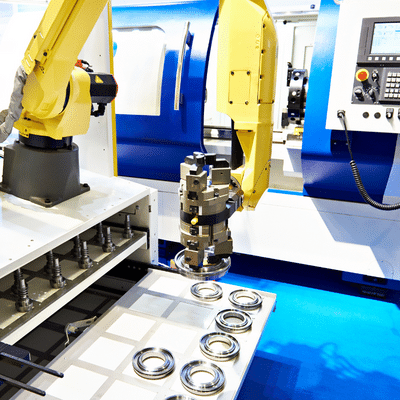
The Ultimate Guide : CNC machining
Evaluating a company’s experience with CNC machining is important to ensure they have the necessary expertise and knowledge to complete projects successfully.
The best way to determine a company’s CNC machining experience is by looking at its portfolio of past projects and reading customer reviews. Ask questions regarding their capabilities, type of equipment used, turnaround time, quality control measures, etc., to get better insight into the company’s CNC machining experience.
Checking a company’s reputation in the industry is essential when selecting CNC machining services.
A good way to gauge their reputation is by seeing what reviews customers have left on third-party websites and evaluating how long they have been in business.
You can also ask for referrals from other businesses or individuals that use the company’s services. Be sure to read industry news and check the company’s website or social media profiles for any awards or accolades they may have received.
Ask the company about their production capacity and turnaround time for similar projects in the past to get an accurate estimate.
Be sure to ask about any potential delays due to equipment malfunctions or other issues that could arise during production.
You should also be clear about your deadlines from the outset so there is no miscommunication when timescales must be met.
Ask the company about their quality control measures, such as in-process and post-process inspections, before production begins.
Be sure to inquire if they use precision measuring instruments and if they have any systems or processes to check for even the smallest defects. These checks and balances can help ensure that your parts meet all necessary specifications and standards.
Please inquire about the qualifications and experience of the operators, along with any specialized training programs they have completed.
Make sure you ask them about their understanding of precision machining and their ability to work with metals, plastics, composites, and ceramics. You want to make sure that your components are produced with quality craftsmanship and expertise every time.
The cost will depend on the complexity and volume of parts required and any additional services needed, such as hard coatings or post-machining processes.
Ask for a quote and compare it to other CNC machining companies to ensure you get the best value for your money. Additionally, make sure that you understand the pricing structure and its upfront costs before agreeing to contracts or orders.
Ask the company about safety measures such as machine guards, warning signs, and evacuation plans in an emergency.
Please inquire about the employees’ experience with CNC machining machinery and their knowledge of safety equipment and machines. Ensure you are satisfied with the safety program before agreeing to any services.
This can help ensure that you receive quality work and that any errors are covered at no extra cost. Consider guarantees such as time frames and acceptable tolerances for parts before making a final decision.
Additionally, some companies may provide additional benefits such as discounts on subsequent orders or free support after the completed service.
Many CNC machining companies offer post-processing services such as heat treatment, plating, and assembly to ensure that parts meet all specifications.
Ask the company if they can provide additional post-processing services, such as surface finishing or grinding, which may be necessary depending on the finished product.
Inquire about any other processes that may be required after machining is complete. Confirm that all services are included in the quoted price before signing a contract.